L’abréviation AMDEC signifie “Analyse des Modes de Défaillances, de leurs Effets et de leur Criticité”. Cette méthode d’analyse des risques de défaillance dans le système est particulièrement adaptée aux usines de production afin d’anticiper tout défaut sur la chaîne de production et de mettre en place des actions correctives rapidement pour traiter la cause avant qu’un incident ne se produise. Comment se déroule une analyse AMDEC Produit ? Quelles sont les étapes de mise en œuvre ? On se penche sur la méthode.
L’analyse des risques
Comme toute analyse des risques conventionnelle on travaille sur des grilles d’évaluation, établies à partir d’échelles de notation comprises entre 1 (le moins dégradé) et 10 (le plus dégradé). Il s’agit d’évaluer la Gravité (G) des effets (aussi appelée sévérité) ; l’Occurrence (O) des défaillances (aussi appelée probabilité d’apparition) ; ainsi que la Détectabilité (D) de cette défaillance (la probabilité de non détection de la cause).
On parle alors de criticité (C) résultante, produit des trois indicateurs précédents.
Criticité = Gravité x Occurrence x Détectabilité
Ainsi la criticité obtient un score compris entre 1 et 1000, nous permettant de prioriser les risques et de mettre œuvre un plan d’actions préventives ou correctives. Prenons un exemple concret pour illustrer une analyse des risques basée sur le produit. Voici les 6 étapes de mise en œuvre d’une AMDEC Produit.
Étape 1 : Description du produit et du processus
Le produit analysé est un moteur électrique dédié à l’industrie automobile.
Le processus de production lié est l’assemblage des composants du moteur (stator, rotor, carter, câblage, etc.)
Étape 2 : Description du groupe de travail
Un groupe de travail pluridisciplinaire va être constitué afin de mutualiser l’ensemble des connaissances et des compétences et ainsi d'avoir une vue d’ensemble du process et du produit. Le groupe de travail peut par exemple être constitué d’un :
- Chef de projet
- Ingénieur qualité
- Ingénieur de production
- Technicien de maintenance
- Responsable de la chaîne de montage
- Opérateur de production
Infographie
5 étapes pour mettre en oeuvre sa cartographie des risques avec l'AMDEC
Télécharger gratuitement notre infographie.
Vous confirmez accepter le traitement de vos données personnelles par BluKanGo, conformément à la Politique de Confidentialité (RGPD) et à recevoir nos communications. Vous pouvez vous désinscrire à tout moment.
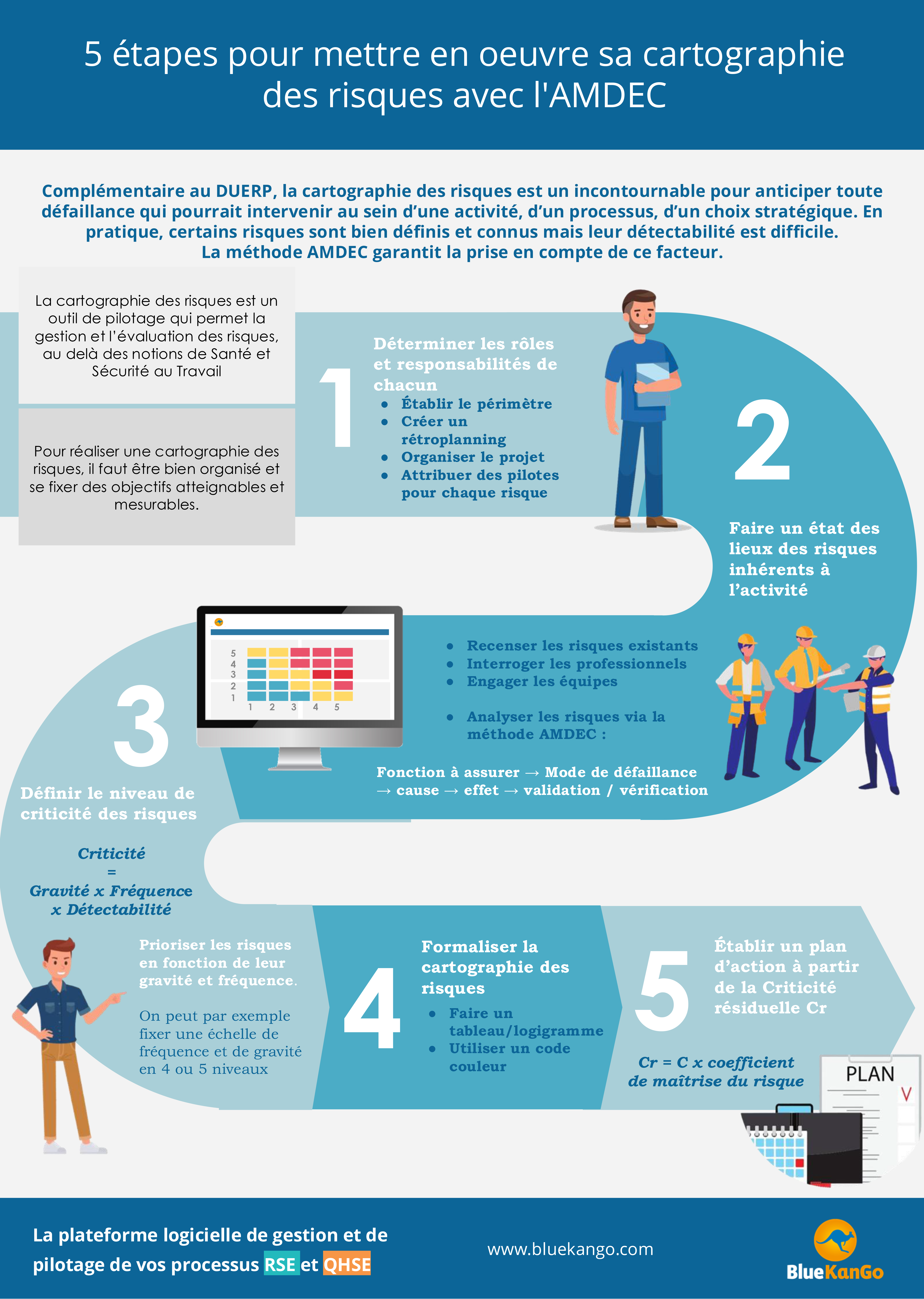
Étape 3 : Identification des fonctions du produit
Il est indispensable de bien comprendre la finalité du produit et son fonctionnement afin de détecter une anomalie dans la chaîne de production.
Ici le moteur électrique doit :
- Générer de l'énergie mécanique à partir de l'énergie électrique.
- Assurer une rotation stable et continue.
- Fonctionner de manière fiable dans diverses conditions de température et d'humidité.
Étape 4 : Décomposition en composants et en étapes de fabrication
A cette étape il est important de décortiquer le produit en composants et en étapes de fabrication / assemblage :
- On retrouve 5 composants principaux :
- Le stator
- Le rotor
- Le carter
- Le système de câblage
- Les roulements
- On peut découper la chaîne d'assemblage en 6 phases :
- L’assemblage du stator
- Le montage du rotor
- L’installation des roulements
- Le câblage interne
- La fermeture du carter
- La phase de tests de qualité
Le même travail peut être réalisé pour prendre en compte les composants du stator et du rotor, ainsi que divers composants secondaires.
Étape 5 : Analyse des modes de défaillance potentiels
Pour chaque composant l’idée est de travailler de manière prédictive sur différents modes de défaillance. Il vient par exemple les résultats (non exhaustifs) suivants :
Étape 6 : Définition d’un plan d’actions
Comme toute analyse des risques, il est nécessaire de définir un plan d’actions préventives et correctives afin d’améliorer les process et gagner en qualité de produit fini. Voici des exemples d’actions :
- Pour le stator : Mettre en place des tests d'isolation plus rigoureux pour détecter les courts-circuits potentiels avant l'assemblage final.
- Pour le rotor : Introduire un processus de calibration et d'équilibrage plus précis pour éviter les déséquilibres.
- Pour les roulements : Offrir une formation approfondie aux opérateurs pour garantir un montage correct des roulements.
- Pour le câblage : Renforcer le contrôle qualité des connexions manuelles pour assurer la fiabilité des connexions.
- Pour le carter : Effectuer des vérifications minutieuses des joints pour éviter les fuites d'huile.
- Pour les tests : Réviser et améliorer les procédures de test pour garantir que tous les aspects critiques sont correctement vérifiés.
N’oubliez pas de définir les moyens humains, matériels et financiers, ainsi qu’un calendrier de mise en place. Des outils de type Gantt peuvent vous aider dans votre gestion de projet lié au plan d’action.
Étape 7 : Revue et mise à jour et suivi d’indicateurs
L'AMDEC doit être revue régulièrement pour prendre en compte les nouveaux retours d'expérience et les éventuelles modifications de processus. Les actions correctives mises en place doivent être suivies pour s'assurer de leur efficacité et ajustées si nécessaire. Mettez en place des indicateurs de performance et de risques (KPI/KRI) pour suivre les performances de vos actions. Vous pourrez ainsi améliorer vos travaux de groupe et être de plus en plus efficace et proactif dans la démarche.
L'analyse AMDEC produit détaillée ci-dessus n’est pas exhaustive, il ne s’agit que d’un exemple. Dans cette étude, elle permet de détecter et d'atténuer les risques de défaillance sur une chaîne de production de moteurs électriques pour automobiles. Cette démarche systématique contribue à améliorer la qualité et la fiabilité du produit final tout en optimisant les processus de fabrication.
. . .