L'AMDEC (Analyse des Modes de Défaillances, de leurs Effets et de leur Criticité) est une méthode d'analyse des risques de défaillance utilisée pour anticiper les défauts dans un système, particulièrement adaptée aux chaînes de production. En se concentrant sur les moyens de production plutôt que sur le produit lui-même, l'AMDEC Moyen, au même titre que l’AMDEC Produit et l’AMDEC Procédé permet de mettre en place des actions correctives avant qu'un incident ne se produise, assurant ainsi la continuité et l'efficacité du processus de fabrication.
Comment se déroule une analyse AMDEC Moyen ? Quelles sont les étapes de mise en œuvre ? Prenons un cas concret.
Dans le cadre de cette étude, nous allons examiner l'application de l'AMDEC Moyen à une chaîne de production de carrosseries automobiles. Cette analyse va retracer les différentes étapes nécessaires pour identifier, évaluer et traiter les potentiels modes de défaillance afin de garantir un fonctionnement optimal et ininterrompu de la production.
Étape 1 : Description du processus de production
Le processus analysé est la chaîne de production de carrosseries automobiles. Cette chaîne inclut diverses étapes telles que le découpage des plaques métalliques, le soudage des composants, la peinture et l'assemblage final.
Étape 2 : Constitution du groupe de travail
Un groupe de travail pluridisciplinaire est formé pour mutualiser les connaissances et les compétences nécessaires à l'analyse. Ce groupe peut inclure par exemple :
- Un chef de projet
- Un ingénieur qualité
- Un ingénieur de production
- Un technicien de maintenance
- Un responsable de la chaîne de montage
- Un opérateur de production
Étape 3 : Identification des moyens de production
Il est crucial de bien comprendre les équipements et les machines utilisés dans la chaîne de production pour détecter les anomalies potentielles. Les moyens de production incluent entre autres :
- La presse à découper
- Les robots de soudage
- Les cabines de peinture
- Les lignes d'assemblage
- Les systèmes de convoyage
Infographie
5 étapes pour mettre en oeuvre sa cartographie des risques avec l'AMDEC
Télécharger gratuitement notre infographie.
Vous confirmez accepter le traitement de vos données personnelles par BluKanGo, conformément à la Politique de Confidentialité (RGPD) et à recevoir nos communications. Vous pouvez vous désinscrire à tout moment.
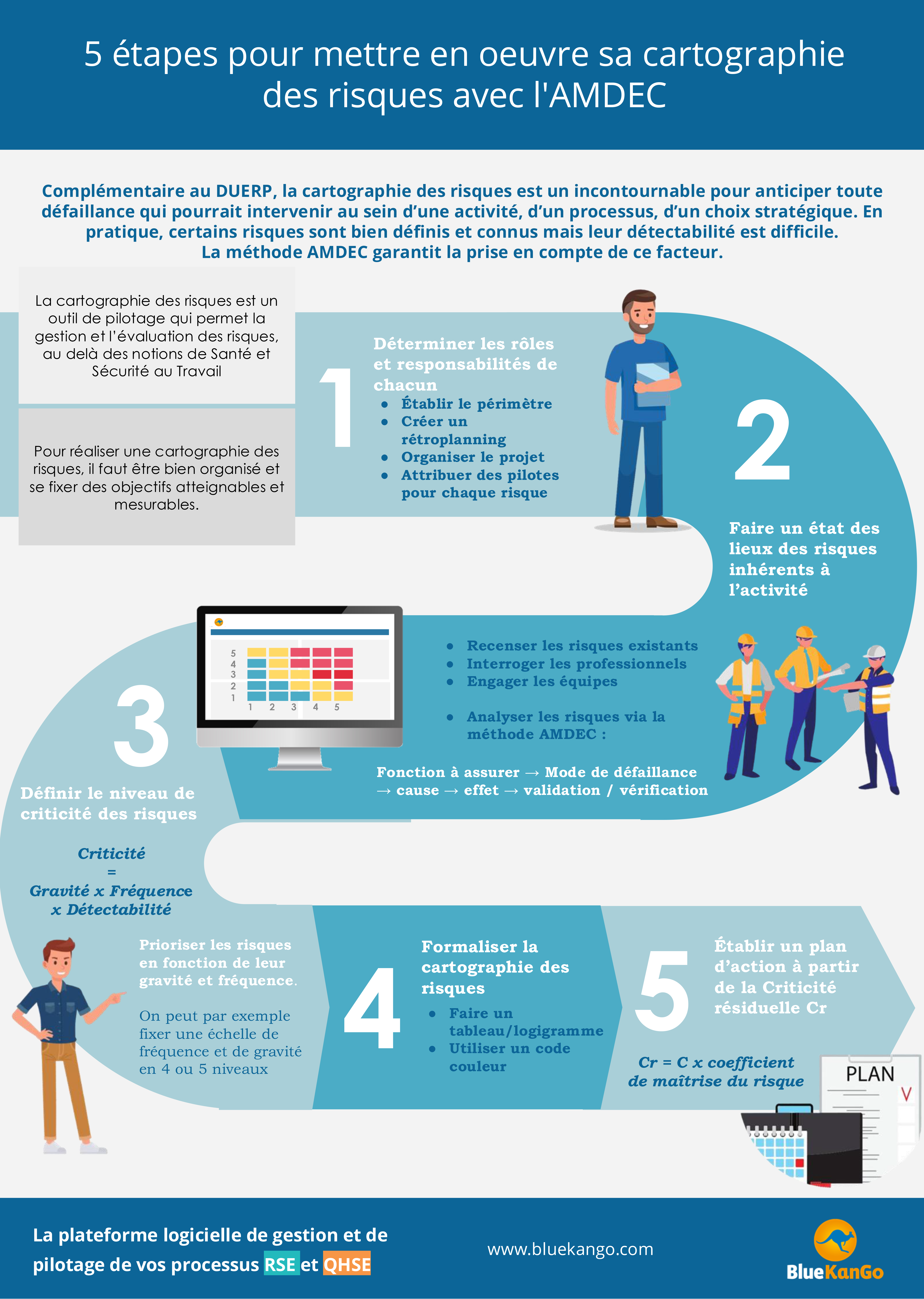
Étape 4 : Décomposition en étapes de fabrication
Chaque moyen de production est décomposé en composants et en étapes de fabrication. Par exemple :
- La presse à découper peut être décomposée en matrices, poinçons, système hydraulique ;
- Les robots de soudage en bras robotisés, source de courant, systèmes de fixation ;
- Les cabines de peinture en systèmes de pulvérisation, filtres, cabines de séchage ;
- Les lignes d'assemblage en convoyeurs, systèmes de serrage, stations de contrôle qualité.
Étape 5 : Analyse des modes de défaillance potentiels
Pour chaque composant et étape de fabrication, différents modes de défaillance potentiels sont identifiés. Voici quelques exemples non exhaustifs :
Étape 6 : Définition d’un plan d’actions
Un plan d'actions préventives et correctives est défini pour améliorer les processus et la qualité du produit final. Voici quelques exemples d'actions :
Étape 7 : Revue, mise à jour et suivi des indicateurs
L'AMDEC doit être revue régulièrement pour prendre en compte les retours d'expérience et les modifications de processus. Les actions correctives doivent être suivies pour s'assurer de leur efficacité et ajustées si nécessaire. Des indicateurs de performance (KPI) et de risques (KRI) doivent être mis en place pour suivre les progrès et améliorer continuellement le processus.
L'analyse AMDEC moyen détaillée ci-dessus permet de détecter et d'atténuer les risques de défaillance sur une chaîne de production de carrosseries automobiles. Cette démarche systématique contribue à améliorer la qualité et la fiabilité du produit final tout en optimisant les processus de fabrication. En suivant les étapes de l'AMDEC, les usines peuvent réduire les arrêts de production, minimiser les coûts de maintenance et garantir une production fluide et efficace.
. . .