L’Analyse des Modes de Défaillance, de leurs Effets et de leur Criticité (AMDEC) est une méthodologie systématique utilisée pour identifier et évaluer les risques associés à des défaillances potentielles dans un processus de production. L'objectif est de prévenir ces défaillances et d'améliorer la fiabilité et la qualité du produit.
Comment se déroule une analyse AMDEC procédé ? Quelles sont les étapes de mise en œuvre ? On regarde de plus près.
Une analyse AMDEC Procédé, au même titre que l’AMDEC Produit, est réalisée par un groupe de travail pluridisciplinaire afin d’avoir l’ensemble des connaissances et des compétences nécessaires à une bonne analyse. La démarche peut se découper en 5 étapes clés telles que définies ci-dessous.
Pour plus de détail sur la création du groupe du travail ainsi que la mise en place d’une grille d’analyse des risques, je vous invite à lire nos articles sur les généralités de l’AMDEC et sur l’étude de cas “AMDEC Produit”.
Voyons à présent les étapes de l’analyse AMDEC procédé.
Étape 1 : Définition du Processus
L’étude de cas va porter comme précédemment sur les processus de production d’un moteur électrique dédié à l’industrie automobile. Ils comprennent entre autres les étapes suivantes :
- Assemblage du Stator
- Assemblage du Rotor
- Assemblage du Carter
- Câblage et Connexion des Composants
- Inspection et Test Final
Étape 2 : Description des Modes de Défaillance Potentiels et de leurs Effets
Chacune des étapes va être analysée pour anticiper tout risque de défaillance.
Assemblage du Stator
- Mode de Défaillance : Mauvais alignement des enroulements
- Effet : Dysfonctionnement du moteur
- Cause Potentielle : Erreur de positionnement
- Détection : Contrôle visuel, test de continuité électrique
- Action Préventive : Utilisation de gabarits d'alignement
Assemblage du Rotor
- Mode de Défaillance : Rotor mal équilibré
- Effet : Vibrations excessives, bruit
- Cause Potentielle : Défaut de fabrication des pales
- Détection : Contrôle d'équilibrage dynamique
- Action Préventive : Inspection rigoureuse des pièces, calibrage des machines
Assemblage du Carter
- Mode de Défaillance : Fuite d'huile
- Effet : Contamination du moteur, risque d'incendie
- Cause Potentielle : Mauvaise étanchéité, défaut de joint
- Détection : Test de pression, inspection visuelle
- Action Préventive : Utilisation de joints de haute qualité, contrôle de la pression d'assemblage
Câblage et Connexion des Composants
- Mode de Défaillance : Connexions lâches ou incorrectes
- Effet : Court-circuit, panne du moteur
- Cause Potentielle : Mauvaise technique de soudure, erreur d'assemblage
- Détection : Test de continuité, inspection visuelle
- Action Préventive : Formation des opérateurs, utilisation d'outils de soudure de qualité
Inspection et Test Final
- Mode de Défaillance : Non-détection des défauts internes
- Effet : Moteur défectueux livré au client
- Cause Potentielle : Test incomplet, équipement de test défectueux
- Détection : Tests fonctionnels et de performance
- Action Préventive : Maintenance régulière des équipements de test, procédures de test détaillées
Infographie
5 étapes pour mettre en oeuvre sa cartographie des risques avec l'AMDEC
Télécharger gratuitement notre infographie.
Vous confirmez accepter le traitement de vos données personnelles par BluKanGo, conformément à la Politique de Confidentialité (RGPD) et à recevoir nos communications. Vous pouvez vous désinscrire à tout moment.
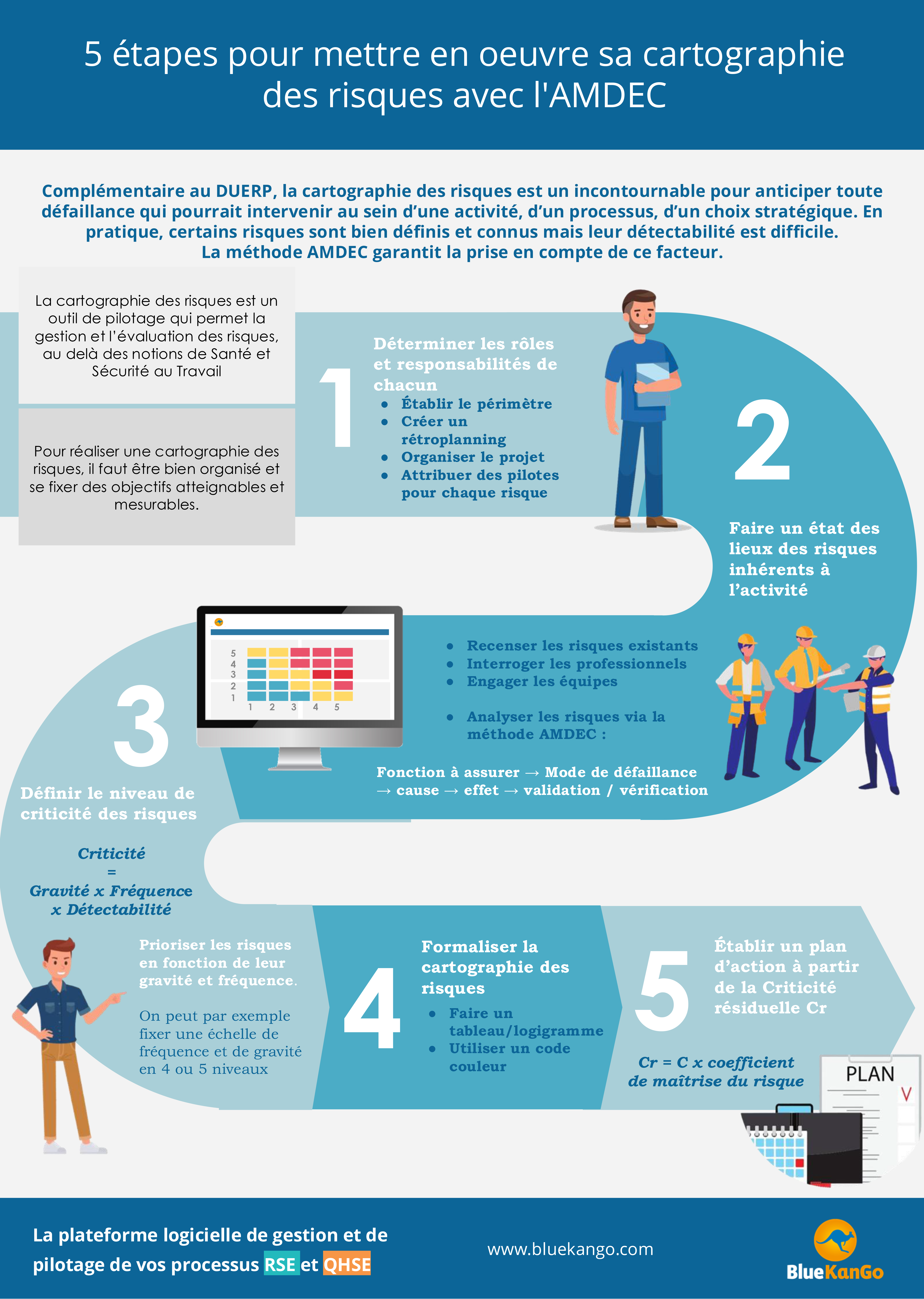
Étape 3 : Évaluation de la Criticité
Chaque mode de défaillance est évalué en termes de Gravité (G), d'Occurence (O), et de Détection (D). La criticité (C) est calculée comme suit : C = G x O x D.
Étape 4 : Mise en place d’un plan d’actions Correctives
Des actions correctives doivent être mises en place pour les modes de défaillance avec les indices de criticité élevés, jugés non acceptables.
Par exemple, on peut se pencher sur les deux défaillances suivantes et proposer une action corrective. Chaque action doit être instaurée avec un objectif bien défini.
- Défaillance 1 :Mauvais alignement des enroulements :
- Action : Améliorer les gabarits d'alignement et la formation des opérateurs.
- Objectif : Réduire l'Occurrence (O) à 2 et la Détection (D) à 3, Criticité (C) visée = 8 x 2 x 3 = 48.
- Défaillance 2 : Rotor mal équilibré :
- Action : Installer un système de contrôle d'équilibrage plus précis.
- Objectif : Réduire la Détection (D) à 3, Criticité (C) visée = 7 x 3 x 3 = 63.
Étape 5 : Suivi et Réévaluation
Après l'implémentation des actions correctives, le processus doit être réévalué pour s'assurer de l'efficacité des mesures prises. Les notes de criticité doivent être re-calculées et des ajustements supplémentaires peuvent être nécessaires si besoin jusqu'à atteindre des niveaux de criticité jugés acceptables par l’organisation.
L'AMDEC procédé pour la production d'un moteur électrique pour automobile permet d'identifier et de prioriser les défaillances potentielles afin d'améliorer la fiabilité du produit et d'assurer une production de haute qualité. La mise en œuvre d'actions correctives adaptées contribue à minimiser les risques et à optimiser le processus de fabrication.
. . .