The ability to control and ensure the quality of products and services is a competitive advantage for companies, it is a way to position them favorably over their competitors and increase consumer interest. Not only must they continually improve their offering to meet market requirements, but they must also implement a quality approach that brings together and organizes all aspects of the company's operation to achieve quality objectives and meet performance requirements.
An action plan lays out the essential actions in the implementation of a structured and effective organization of the quality approach.
How to set up a global action plan? What are the benefits?
The implementation of a quality approach involves all companies’ stakeholders, a collaboration that requires an organized and structured implementation. The action plan is the reference in terms of piloting and coordinating actions. It is a part of the “Plan” stage of the PDCA or commonly known as the “Deming wheel”, and constitutes an essential gateway to the implementation of a structured and effective quality approach.
Let's see how a global action plan can be the key to achieving the objectives of the quality policy.
What is an action plan?
An action plan is a tool for planning the key actions to be implemented in the company to achieve the objectives set by the management and the Quality and HSE policy. It formalizes and lists the various actions to be carried out within the organization. It consists of a number of actions to be deployed, the associated pilots, the necessary means, as well as the deadlines for completion.
Generally established over one year, an action plan has to be renewed and updated each year. Indeed, over several years, actions can be poorly monitored or even neglected. Whereas if the actions are defined for one year, this demands the pilots to follow them regularly.
The implementation of a global action plan is a team effort, it is important to reiterate that this requires the involvement of all stakeholders. Each employee must feel involved in the process!
Why should you use a global action plan?
Taking the time to prepare and establish a plan before any endeavor or undertaking has been common practice for a long time. As America's Founding Father Benjamin Franklin would say:
“By Failing to prepare, you are preparing to fail.”
Because no organization wants to fail, it makes sense to take whatever steps are necessary to ensure success, including developing a good action plan. There are many reasons to think through the details of your organization's actions in an action plan, here are some of the most relevant:
- The organization can prioritize actions and understand what is and what is not possible to do.
- Demonstrate the credibility of the organization: an action plan shows investors and customers that an organization is well ordered and committed to achieving its objective.
- Ideas are better organized, and it makes sure that there is any detail overlooked.
- Time and resources are optimized and most difficulties are anticipated.
- Improve efficiency in the long run.
The action plan thus offers the possibility of having a detailed plan of actions to be implemented and completed over an entire year, with of course the involvement of the process pilots and managers concerned. Remember, people don't plan to fail, instead they fail to plan.
How to create an Action plan?
When developing an action plan, you need to focus on each component of each action step towards the main objectives. Therefore, the action plan should include data and insights that have been gathered while brainstorming organizational goals and strategies. The overall plan must be clear, complete, and up to date.
Define the list of steps to complete to achieve the quality objectives and meet the performance requirements. While the overall plan addresses the general goals to be accomplished, the action steps determine the concrete actions needed to turn those goals into reality.
It is a procedure that must be done methodically, and step by step.
Step 1: Inventory the existing situation
This inventory process involves the management board, which must know the results of the actual inventory and resources of the organization and the internal/external context, to build the Quality and HSE policy.
Step 2: Define the objectives
When the Quality and HSE policy has been defined, the next step is the strategic analysis using a SWOT or PESTEL analysis method. This analysis will generate measurable objectives in line with the strategy.
Step 3: Formalize the actions plan
Once the objectives have been established, it is now time to put in place actions dedicated to achieving them. Each process pilot, with his team, has to define the list of actions to be carried out during the year. At this stage, the Quality and HSE managers have the role of the project manager, helping the pilots to formalize their actions.
The validation of the action plan is done by a management review. This is a stage that demonstrates the management's commitment in terms of the resources allocated varying from equipment investment, purchase of premium raw materials, human resource needs, etc.
Step 4: Building up the action plan
To build a global action plan, there is various structure and supports you can use, but there is some essential information that has to be included:
- The action description;
- The status (not started, in progress, validated, etc.);
- The degree of criticality (according to the organization’s criticality matrix);
- The starting date;
- The planned end date and the actual end date;
- The associated manager(s)/pilot(s);
- The level of priority (low, medium, high, very high).
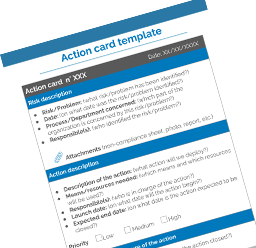
Recommended for you. Download our free "Action Form Template"
A digital platform to manage the global Action plan
Almost every team these days uses some type of project management software to manage their action plan. Indeed, to ensure effective follow-up of the action plan, it is preferable to use different project management methods such as the GANTT diagram. A process that allows you to visualize the different actions to be carried out over time, but also to graphically represent the progress of a project.
In the digital age, there are dedicated platforms that allow you to manage your Global Action Plan in collaboration with all of your process pilots. If your team has used a project management software or tool before, they for sure know that it helps tremendously in planning, executing, and tracking projects.
Here are the main features that make the strength of an effective global Action plan digital platform:
- A centralized dashboard: Access holistic views of everything in your organization in real-time. With a centralized dashboard, you can use customizable widgets to get important information about employees, projects, tasks, etc.
- Customized display: if you have a preference in the way the dashboard is displayed, you can customize it in a List, Box, Gantt chart, Board, Table, or Calendar view using drag and drop.
- Workflow management: The workflow can be easily managed using filters. It is thus possible to evaluate the current workload of each process pilot. A convenient feature for managing a team remotely.
- Assign tasks: Easily assign tasks to the right person and set specific timelines, milestones, due dates, follow-up dates and times, and dependencies.
- Priorities: When the person in charge of several actions does not know which tasks are the most important, this technology allows personalized priority levels and correlation on various tasks according to their urgency and importance.
- Reminders/Alert/Notification: This feature will ensure that important tasks, start dates and due dates are not forgotten. Users will be able to receive notifications by email or directly on their mobile devices (smartphones and tablets).
- KPIs: Define KPIs for each process. It can also be used to set weekly and monthly sprint goals.
There are no limits to the possibilities and options of these new technologies. By delegating responsibilities to those responsible for each action, this tool definitely involves everyone in the company in the implementation of the quality approach.
The Action Plan is an essential tool in the QHSE field, although it can also be used in other departments, and for other purposes. It is a question of being vigilant and meticulous to make sure not to multiply the number of action plans so as not to create a time-consuming system. The implementation of digital solutions frees the Quality and HSE Managers from actions with low added value, and the pilots gain in efficiency by avoiding multiple transcriptions.
Learn more:
> Global Quality, HSE, multi-site and multi-activity actions plan
. . .