Awareness, anticipation, and hazard elimination at the source are crucial elements for risk prevention in a company. However, incidents and accidents can still occur, and identifying their possible causes becomes necessary. This is where the “Causal Factor Tree Analysis” (CFTA) comes in as an effective risk management tool to thoroughly analyse the causes and sequence of actions that may have contributed to the incident and determine the necessary preventive measures to avoid unwanted events.
What is Causal Factor Tree Analysis all about? How is the CFTA applied in companies?
Let us go through the details in this article.
Causal Factor Tree Analysis: Definition & Objective
Causal Factor Tree Analysis (CFTA) is a structured analytical technique used to identify and analyse the causal factors that contribute to a particular event, accident/incident, or outcome, focusing on safety, risk management, and accident investigation.
This risk management tool involves constructing a graphical representation of the event, placing the outcome at the top of the tree and the various causal factors arranged as branches below it. Each causal factor is then broken down into sub-factors, which may themselves have additional sub-factors, and so on until the root causes of the event are identified.
The main objective of CFTA is to provide a methodological and thorough approach to understanding the factors that contributed to the accident/incident, enabling appropriate actions to be implemented to prevent and mitigate the likelihood of similar incidents.
In general, this tool is commonly used in high-risk industries, like aviation, nuclear power, and chemical manufacturing industries, however, it is also applied in many other industries where a thorough understanding and investigation of accidents/incidents is required. Therefore, it remains a widely used risk management tool by many industries.
Practical Application of CFTA
Three main steps allow the successful build-up of the CFTA.
It all starts with the collection of factual information and data related to the incident. Everything should be looked into thoroughly in chronologically classified. Afterwards, you build the graphical representation of CFTA, by detailing all the descriptions related to each event, contributor and environment. And finally, when all is analysed and comprehended, you can proceed to the implementation of corrective actions to mitigate all the related risks at each event level if necessary.
You must keep in mind that for the CFTA to succeed, you must rely on a multidisciplinary working group that will conduct all the collection, analysis of data and investigation. In addition, for each event, the date and time are attributed.
Step 1: Factual Data Collection
This step is crucial for the working group, and they must start as early as possible. Gathering all the necessary information, and all the conditions related to the event are essential to build the CFTA afterwards.
The team builds up a checklist investigation form to cover all the conditions, primary events, and sub-events that lead to the accident. If possible, the investigation can start with the victim himself, if there are any. This is important for determining the first consequences of the accident. From then on, the investigation starts to trace upward to identify the root causes of the event.
When the team conducts the investigations, the risk assessment of each task should be carefully looked into to determine the conditions leading to each related event and sub-event. Moreover, testimonials are gathered from witnesses and managers on-site, in addition to all the working procedures, equipment and maintenance schedules if necessary. Therefore, one of the important team members is the HSE professional where checking the compliance of the working conditions with internal protocols is highly important. In addition, the working group must gain access to all the records (medical, training, etc.) related to the concerned workers and the event.
Gathering testimonials for witnesses and team managers is no easy task. The investigation team must remain factual, collect testimonies, not thoughts and feelings, and remain objective.
Finally, when all the primary factual data is collected, the team can start building the event tree chronologically, and they might have some holes in the succession of events. Striving to fill these gaps and achieve precise tracing of event sequences and their derivation from contributory conditions will prompt the team to conduct more thorough investigations, ultimately revealing the facts.
Step 2: Building the CFTA
Once the factual data is collected, and all the gaps are filled, the team proceeds to build the CFTA’s graphical chart. It is important to represent step by step, each event leading to the other. Main events are highlighted and connected with solid arrows. In addition, all the secondary events and conditions leading to each event must be also connected to the latter. Every box representing an event or a condition must be thoroughly described.
The CFTA tree is dressed chronologically, with the top event on the far right or top and the resulting incident/accident on the bottom or the left side of the diagram.
When the visual representation is done, the team can see where all the necessary corrective actions must be implemented, and issue the final report.
Step 3: Corrective Actions and Associated Preventive Measures Implementation
When the incident/accident has occurred, direct and quick actions must be taken and establish primary preventive measures to avoid any other consequences.
Returning to the diagram, corrective actions must be taken at each related event to eliminate the related risks. If the risks of a secondary or middle event in the tree were already mitigated, the accident/incident could have never occurred.
The new corrective actions must comply with the internal procedures and external regulations, be based on a thorough risk assessment, be stable over time, maybe even provide additional training for employees, implementations deadlines, and must be frequently reviewed and updated.
Causal Factor Tree Analysis Application Example
A lab technician ended up in a hospital ER after deeply cutting their hand with a sharp material. The incident occurred in an environmental testing laboratory when the lab technician was preparing the sample to be analysed for asbestos search in its composition.
Factual data collection
The investigation team went on to the working site and interviewed the victim after he got back from the ER. The team directly noted the time and date of the incident and listened to the testimony of the lab technician. When he was cut, the team manager tried to look for the first aid kit and did not find it, and called out to the first aider on site. The first aider took the lab technician out of the laboratory to the manager’s office and found the first aid kit. Unfortunately, they found some expired medical equipment in the first aid kit. Therefore a small bandage was put and the lab technician was accompanied to the hospital by the first aider.
The team took that first factual information, started building up the CFTA chart, and drew up all the events and conditions leading to the accident. Afterwards, the team provided the corrective actions based on their assessment.
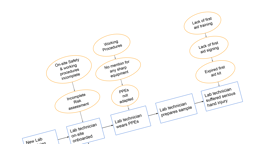
Recommended for you. Download our free "a CFTA chart example"
The main identified deviations and causal factors:
- Lack of First aid kit review
- No signs for first aid place identification
- Lack of manager training in handling this sort of incidents
- No mention whatsoever about the use of sharp material in the working procedures
- Gloves not adapted to sharp equipment.
- The major causal factor: lack of risk assessment update
Corrective actions:
- Update the working procedures to include all used equipment during the sample preparations
- Update the risk assessment according to the new working procedures
- Adopt new PPEs better suited for each task
- Update the training and onboarding programme
- Regularly check the first aid kit
- Train employees on emergency procedures
- Put in place clear signs indicating the location of the first aid kit
Once all is set, it is important to communicate all the updates related to the corrective actions and ensure that all concerned stakeholders know the new measures.
It is essential to critically evaluate accidents analysed by understanding the facts and reassessing risk assessment matrices to include new risks. All organisations rely on accident analysis tools to identify weaknesses and prevent occupational hazards. Therefore, most HSE departments typically use the CFTA approach, to thoroughly investigate incidents and accidents. An effective risk prevention plan can greatly benefit from this approach, which can help with fast decision-making and fast implementation of corrective actions.
For enhanced incident and accident reporting and record-keeping discover
. . .